또 시간을 생각한다. 나는 뜻밖의 장소에서 시간을 찍어내는 거푸집을 찾아내곤 했다. 이번에도 그런 기대를 품고 CJ대한통운의 군포 스마트 풀필먼트 센터(군포 FC)로 가는 길이다. 다른 회사의 상품을 보관하고 있다가 소비자의 주문이 들어오면 포장하고 출고해 곤지암, 대전, 청원 같은 지역별 허브로 보내주는 물류센터다. 매일 약 4만 명이 이 센터를 거쳐 간 택배 상자를 받아든다.
이 업의 본질 역시 누군가의 시간을 절약해주는 일이다. 이제 모두의 일상이 된 전자상거래의 공급자와 수요자 모두 이 물류센터 덕분에 더 많은 시간을 일하고 놀고 공부하고 여행하고 멍때릴 수 있을 것이다. 즉석 밥이나 냉동 만두 공장에서도 그런 시간을 만들어내고 있었다. 우리가 택배 상자와 함께 받아드는 시간은 제조회사가 찍어낸 시간에 물류회사가 짜낸 시간을 더한 것이다. 하지만 김이 모락모락 나는 밥이나 만두를 앞에 놓고 물류회사를 생각하는 이는 거의 없을 것이다.
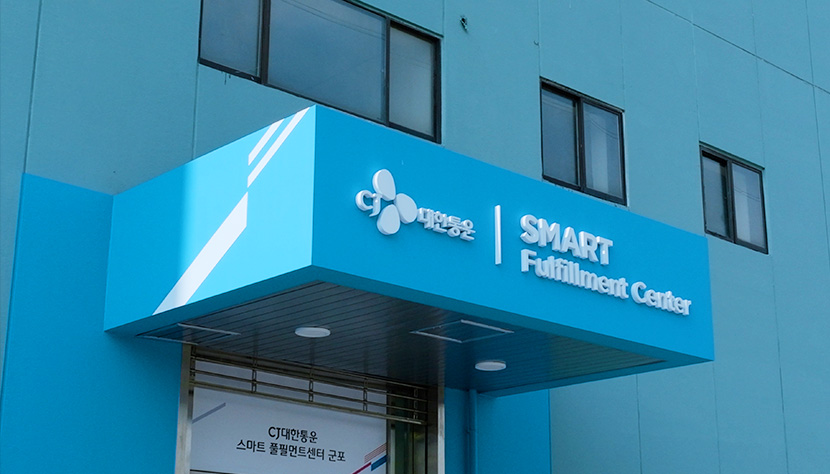
군포 복합물류센터의 넓은 도로 양쪽에 줄지어 선 건물들. 소비자와 직접 만나지 않는 건물은 화장기 없는 얼굴이다. 하나같이 단순하다. 벽면의 알파벳과 숫자로는 정체성이 잘 드러나지 않는다. 우리가 잠든 사이에도 묵묵히 일하는 충직한 일꾼의 모습일까?
CJ대한통운 군포 FC는 5층 건물이다. 연면적이 1만1000평을 넘는다. 저 안에 쌓여 있는 상품들은 누군가가 살아갈 에너지가 될 것이다. 어떤 이는 일상용품을 잠결에 받아들고 어떤 이는 예상 못 한 선물에 깜짝 놀라겠지. 저 안에는 어떤 사람과 기계가 일하고 있을까? 영화에 나오듯이 온갖 형상의 로봇들이 분주히 짐을 나르고 있을까? 스마트 풀필먼트 센터라면 똑똑한 물류센터라는 말이다. 얼마나 똑똑하길래 이런 이름을 붙였을까?
이곳에서는 물류센터가 어떻게 진화하고 있는지 한눈에 알 수 있다. 색깔이 다른 지층은 지질학자가 아니어도 한눈에 알아볼 수 있다. 이 물류센터의 한 층은 그런 지층처럼 방문자의 눈에 확 띈다. 2층은 특별히 스마트 층으로 불린다. 일반층보다 더 똑똑하게 일한다는 뜻이다.
그 결과는 생산성 지표로 나온다. 일반층의 2000평 작업장에서 하루에 출고되는 상품은 평균 7400상자다. 스마트 층은 같은 면적에서 그보다 35% 많은 1만 상자를 출고한다. 일반층에서 한 사람이 한 시간에 출고하는 상자는 평균 열일곱 개 남짓한 수준이다. 스마트 층에서는 한 사람이 시간당 스물네 상자를 출고한다. 많게는 서른두 상자까지 처리할 수 있다.
군포FC의 책임자인 조주형 센터장은 이곳을 설계할 때 “유연한 자동화, 무인화와 지능화, 상시 최적화”를 추구했다고 말한다. 전자상거래로 파는 상품들이 다양해질수록 물류에 시간과 비용이 많이 든다. 숙련된 작업자는 갈수록 구하기 어려워진다.
그럴수록 생산성을 높여 시간과 비용을 아끼는 수밖에 없다. 주문이 들쭉날쭉한 만큼 언제나 유연하게 대응할 수 있는 시스템을 갖춰야 한다. 그 논리는 쉽게 이해된다. 그렇다면 어떻게 생산성을 높이고 있을까? 금쪽같은 시간을 짜내는 비결은 뭘까?
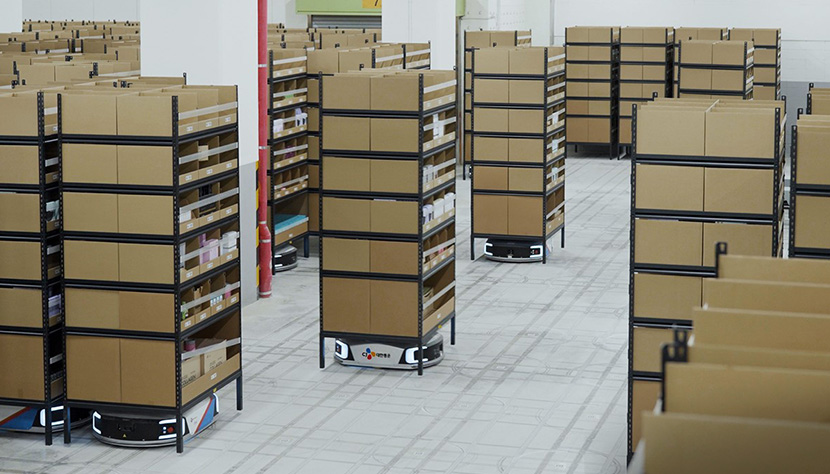
물류센터의 출고 작업은 먼저 쌓여 있는 상품 중에서 소비자가 주문한 것을 골라서 가져오는 것으로 시작된다. 피킹 작업이다. 일반층에서는 작업자가 직접 카트를 끌고 넓은 작업장을 돌아다니며 특정한 위치에 있는 상품을 일일이 골라 와야 한다. 스마트 층에서는 AGV(고정 노선 운송 로봇)가 그 일을 대신한다.
상품은 작은 책장처럼 생긴 선반에 미리 올려져 있다. 작업자는 컴퓨터 화면이 있는 피킹 스테이션에 서서 주문한 상품을 가져오라고 AGV에 지시한다. 조금 큰 청소 로봇처럼 둥그렇게 생긴 AGV가 선반을 들고 작업자를 찾아온다. 작업자가 해당 상품을 선반에서 내려 상자에 담아주면 또 다른 AGV가 검수대로 옮겨간다.
11곳의 피킹 스테이션에서 일하는 작업자는 두세 발만 움직이면서 모든 일을 처리한다. AGV는 작은 체구에도 1톤까지 들 수 있고 길을 잃는 법이 없다. 서로 부딪히지도 않는다. 배터리가 소진되기 전에 스스로 충전기를 찾아간다.
스마트 층에는 피킹과 이송 작업을 하는 126대의 AGV가 말 잘 듣고 똑똑한 짐꾼이 되어 준다. 짐꾼은 힘이 세고 지칠 줄 모른다. 이들을 부리면 컨베이어벨트 같은 고정형 설비를 이용하는 전통적인 방식보다 공간을 더 효율적으로 쓸 수 있다. 작업 물량 변동이 심할 때도 유연하게 대응할 수 있다.
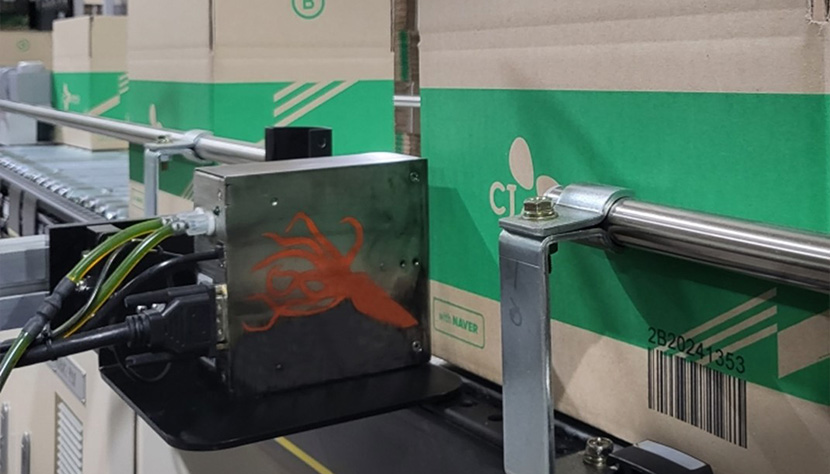
도우미는 곳곳에 있다. 체적 측정기는 상품 데이터를 단숨에 수집해 활용할 수 있게 해준다. 가로세로와 높이는 물론 생김새까지 정확히 파악해 아홉 가지 상자 중에서 가장 알맞은 출고 상자를 정해준다. 눈대중으로 할 때보다 시간과 자원 낭비를 줄일 수 있다.
바코드 프린터는 오징어가 먹물을 뿜듯 상자에 바코드를 찍어준다. 분리배출 때 바코드 스티커를 떼어내느라 애를 먹은 이들은 이 방식이 얼마나 친환경적인지 알 수 있을 것이다. 중량 검수기는 사람이 해야 하던 검수 작업을 무인화했다. 상자의 바코드를 읽고 엉뚱한 상품이 들었거나 개수가 달라 상품 무게의 5% 오차 범위를 벗어나면 제깍 걸러낸다.
수작업으로 하던 포장도 로봇이 다 알아서 해준다. 적당한 상자를 고르고 접을 때부터 포장을 마무리해 운송장을 붙일 때까지 로봇이 전부 알아서 해준다. 3D 스캐너를 통해 완충재를 꼭 필요한 만큼만 넣어주므로 파손이나 낭비를 줄일 수 있다. 운송장이 붙은 상자는 스파이럴 컨베이어를 타고 1층으로 내려간다. 휠소터는 상자가 제 갈 길을 찾아 지역별 허브 터미널로 출고되도록 분류해준다.
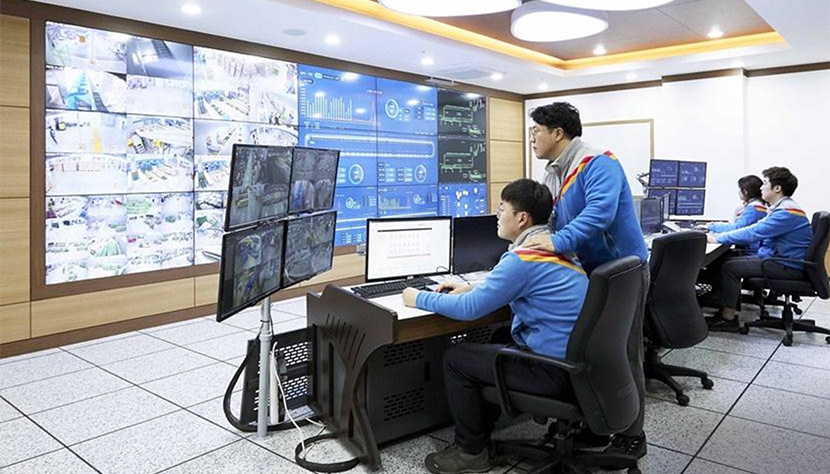
종합 관제실은 이 모든 과정을 실시간으로 모니터링하고 분석한다. 로봇이나 지게차의 움직임을 포함해 현장의 모든 상황은 가상 공간에 고스란히 재현된다. 디지털 트윈이다. 현장의 리스크를 사전에 탐지할 수 있고 작업자의 빠른 의사 결정을 도와줄 수 있는 시스템이다. 주문과 재고 상황도 실시간으로 알려준다. 오래된 재고는 빨간 색으로 표시돼 처분을 기다린다.
모든 일은 시간과 싸움이다. 이 물류센터의 서비스는 고객 주문이 들어오면 24시간 안에 배송을 완료하는 것이다. 매일 아침 9시부터 다음날 새벽 3시까지 모든 작업을 마치고 각 지역 허브로 보내야 아침 5시부터 분류 작업을 할 수 있다.
도착 날짜를 보장하려는 수백 곳의 판매자들 요구에 맞추려면 유연한 자동화와 무인화·지능화, 상시 최적화를 지상 명령처럼 여겨야 한다. 전자상거래의 속도 경쟁은 갈수록 격화할 것이다. 이미 토요일에 주문하면 일요일에 받아볼 수 있게 하는 서비스까지 나왔다. 시간과 싸움은 얼마나 더 치열해야 할까?
생산성 제고의 압박감이 그토록 크다면 모든 것이 자동화되고 사람 한 명과 개 한 마리만 지키는 미래의 공장이 곧 현실로 닥치게 된다는 뜻일까? (1화. 햇반 공장에서 다시 묻는다 “밥은 먹었니?” 참조)
아닐 것이다. 물류 기술 진화에서 가장 앞서 나간다고 할 수 있는 이곳에서도 자동화율은 약 70% 정도다. 조주형 센터장은 “자동화는 어디까지나 사람이 더 많은 일을 할 수 있게 도와준다는 개념”이라고 말한다. TES 물류연구소 DT기술팀의 최태진 엔지니어는 “여전히 어떤 일에서는 로봇의 생산성이 사람보다 안 나온다”고 말한다.
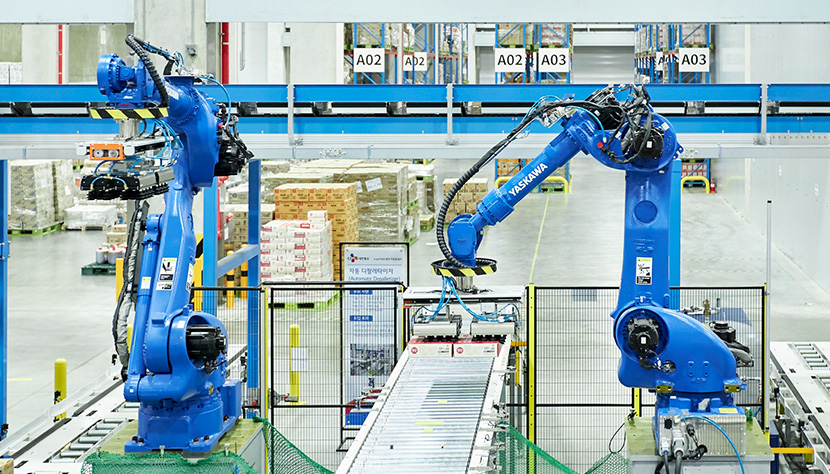
예컨대 피킹 작업 때 온갖 물성을 지닌 상품들을 보자마자 전체적으로 판단해 중심점을 잡고 들어 올리는 작업은 사람이 더 잘할 수 있다. 맥주 캔보다 연약한 물건이나 고가의 평면 TV처럼 조심해서 다뤄야 할 상품을 다 로봇 팔에 맡기기는 어렵다.
우리는 한 치의 빈틈도 없이 움직이는 로봇이 사실 물렁물렁한 바나나를 잘 집어 들지 못한다는 것을 안다. 상품을 피킹하고 짐을 차에 싣고 트럭을 모는 일까지 인공지능 로봇이 하기까지는 아직도 상당한 시간이 걸릴 것이다. 물류 기술에서 최첨단을 달리는 미국에서도 로봇이 피킹 작업을 익히기까지 10년이나 15년이 더 걸릴 것이라는 기사가 생각난다.
물류 기술 진화는 하루아침에 이뤄진 것이 아니다. 20세기의 대량생산 체제를 상징하는 것은 포디즘이다. 포디즘을 상징하는 것은 컨베이어벨트다. 헨리 포드는 시카고의 육가공업체도 가보고 우편 주문 판매업체도 가봤다. 그곳의 컨베이어벨트에서 물 흐르듯 이어지는 조립 공정의 아이디어를 얻었다. 시어스 로벅의 물류창고에서 본 엘리베이터와 컨베이어와 활강로에서 노동력과 시간을 줄일 기술을 포착했다. 작업자가 움직이지 않고 차가 움직이는 조립 방식은 혁명적 변화였다. 포드는 ‘모델 T’처럼 똑같은 차를 대량으로 찍어내는 방식으로 생산성을 높였다.
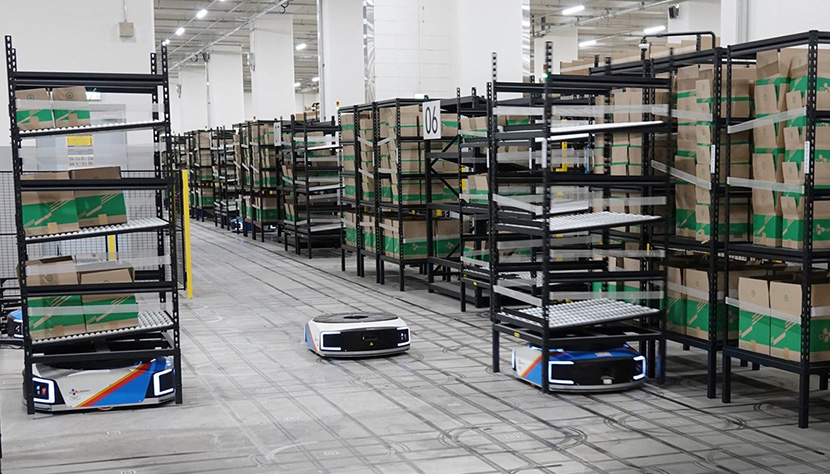
오늘날 유통 혁명의 한 축인 물류센터는 그런 발상을 뛰어넘고 있다. 물류 시스템은 수백, 수천 가지 상품을 다뤄야 하므로 그만큼 더 유연하고 똑똑해야 한다. 컨베이어 같은 고정형 설비는 움직이는 로봇으로 대체되고 로봇처럼 기계적으로 움직이던 작업자는 로봇을 부릴 수 있는 기술자로 변신하고 있다.
AGV나 디지털 트윈 같은 기술은 또 다른 물류 혁명을 낳을 것이다. 그 혁명의 요체는 새로운 시간을 창조하는 것이다. 그 덕분에 나는 이 가속의 시대에도 조금 더 편히 잠들 수 있겠지.

장경덕 | 작가·번역가
33년간 저널리스트로서 경제와 기업을 탐사했다. 『애덤 스미스 함께 읽기』 『정글경제 특강』 등을 썼고 『21세기 자본』 『좁은 회랑』 등을 옮겼다.